Start-ups: significant achievements reached in first half of 2016
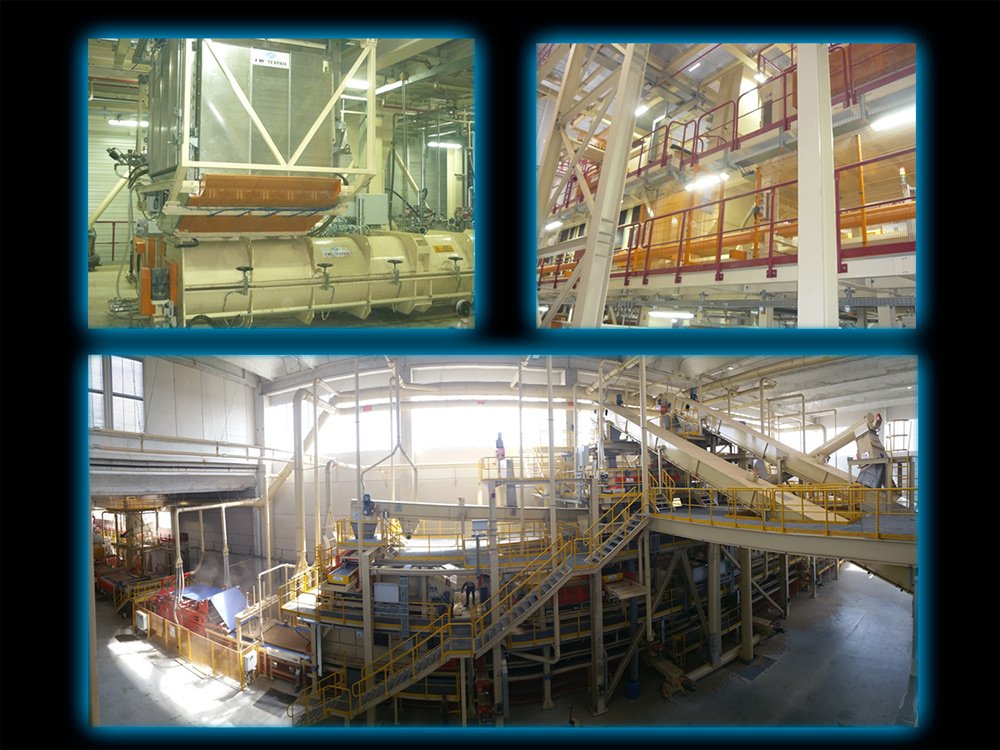
The first half of the year had a very positive outcome for CMC TEXPAN.
Two important projects were successfully started-up in the last months, both in Europe: "Rauch Spanplattenwerk" (Markt Bibart, Southern Germany) and "Saib" (Fossadello di Caorso, Northern Italy).
"The first of these projects represented a great challenge for our company" states Daniele Panzeri, Technical and Technological Director at CMC TEXPAN. "Our supply included EcoResinator and EcoFormer, our recent innovations dedicated to glue blending and respectively mat forming. The first EcoFormer (installed in a Russian plant) has been operating since the beginning of 2015 to the full satisfaction of the customer, therefore no doubt about the quality and efficiency of this system."
"The key point of this particular project was represented by the extensive, multi-stage series of tests that our machinery had to undergo according to customer specifications" continues Mr. Panzeri "This required a major effort by our whole team and I'm glad to say that the plant is currently operating at full capacity and the first stage of quality tests gave positive results: the stringent forming accuracy required by the customer has been achieved. We are now entering the second test phase with confidence and renewed commitment".
The implementation of the glue blending and forming system at the "Saib" plant is not less important. The Italian panel manufacturer is a long-time customer of CMC TEXPAN and, once again, chose the Siempelkamp group to equip his facility, located some 50 km south of Milan, with a new forming and pressing line for particleboard. The challenge, in this case, was represented by the specific target of the project: producing high quality particleboard using 100% recycled wood as a raw material. The production line received a Siempelkamp 8' x 30.5 m ContiRoll® press, while CMC TEXPAN's supply included glue blenders and a four-head forming station in traditional execution with integrated weighing systems (built-in scales for particle dosing bins and mat scale at forming line outlet). In this project, the well-established partnership between customer and supplier represented a further help to a smooth, timely and effective accomplishment of the whole erection and start-up procedure.